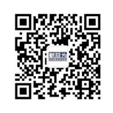
微信公眾號二維碼
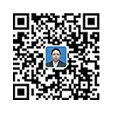
微信咨詢顧問二維碼
新益為TPM管理咨詢公司概述:在各類設備管理模式中,TPM作為由日本傳入中國的維護模式在制造業(yè)生產線廣為應用。隨著企業(yè)生產線智能化改造不斷增加,對于巡檢效率、巡檢數據匯總方式、巡檢信息傳遞時效性提出更高要求。
TPM管理咨詢
我們行業(yè)有一個普遍的誤解:TPM(Total Productive Maintenance)是精益生產的一部分。事實上,兩者原本是兩個獨立的改進管理系統(tǒng)。但實踐證明,兩者除了互補互通外,還可以而且必須徹底融合。
由于生產工藝要求,很多企業(yè)天生就是設備密集型的;此外,由于勞動力成本上升和人員流動性大,中國企業(yè)普遍從勞動密集型智能制造轉向裝備密集型智能制造。降低成本,穩(wěn)定生產,提高效率,創(chuàng)造更多更好的價值。
然而,設備密集型企業(yè)往往存在故障、產品故障、安全事故、環(huán)境污染等諸多問題,直接影響經營業(yè)績。企業(yè)在提升經營業(yè)績時,一般選擇單靠精益生產或單靠TPM管理,但即使認真實施,最終也會發(fā)現(xiàn),雖然有一定的提升效果,但也存在明顯的不足。為什么?
在設備密集型企業(yè)中,企業(yè)的整體效率和經營業(yè)績嚴重依賴生產設備。如果只實施精益生產,往往缺乏對設備管理的必要深度和系統(tǒng)化改進,無法實現(xiàn)零故障。OEE提升等核心目標。例如:在設備自主維護、專業(yè)維護等方面,如何有效開展“定期維護”、“狀態(tài)維護”、“維護預防”、“設備自愈功能”等,精益生產理論沒有。一旦設備處于有病運行的狀態(tài),精益生產所強調的移動生產、穩(wěn)定生產、零庫存將是徒勞的。
反過來說,即使是設備密集型企業(yè),設備自然是主要的管理對象,但遠非唯一的管理對象。如果單獨實施TPM管理,由于TPM管理主要針對生產設備,往往容易以設備討論設備,失去整體視野和改進機會。例如,如果要識別一個企業(yè)的整體效率,精益生產中的價值流分析是一種理想的方法,但TPM管理不涉及價值流分析;再比如,在一些設備密集型企業(yè),實行單件流轉、均衡生產、自働化等,可以顯著提高生產效率、產品質量、降低成本,但TPM并未深入參與。另外,如果企業(yè)整體經營的瓶頸不在于生產設備的效率,而在于其他方在這種情況下,根據高德拉特的“TOC”原理,我們不難判斷:如果還堅持實施TPM管理,對提高企業(yè)整體效率的意義是非常有限的。
1983年,“TPM之父”中島清一先生闡述了精益生產與精益TPM的互補互通關系;1988年,他寫了一篇文章,提倡精益生產與精益TPM的融合,希望能一元化地開展,近年來,在與很多企業(yè)從業(yè)者就此進行交流時,也認為有必要將兩者有機地融合起來。
根據中島清一先生的啟示,如果將精益生產和TPM管理有機地結合成一個“精益TPM”體系,1+1>2的效果是可以預期的。針對設備密集型企業(yè)的特點,在運用精益TPM管理提升企業(yè)經營績效時,要把握兩條主線,缺一不可。
從業(yè)務運作的角度來看,應該涵蓋產品生命周期的各個環(huán)節(jié),包括營銷、產品規(guī)劃、設計開發(fā)、生產規(guī)劃、采購、產品實現(xiàn)、交付、使用、售后服務、退役、回收、工藝以及質量控制、倉儲和物流、安全、環(huán)保、行政人員和其他職能流程。
同時,從設備集約化的角度,必須涵蓋設備生命周期的各個環(huán)節(jié),包括設備規(guī)劃、設計、選型、購置、安裝、調試、驗收、使用、維護、維修、技改、退役等等。
企業(yè)應根據自身特點規(guī)劃、實施并持續(xù)改進“精益TPM”。另外值得一提的是,市場上很多宣傳的“精益TPM”其實就是TPM,只是趕上潮流,掛了一個“精益”的名字。這個偽“精益TPM”并沒有真正把精益和TPM結合起來,基本不涉及精益的重要內容,比如缺少單件流、標準作業(yè)、均衡生產、看板拉動、自働化。
市場在不斷變化和創(chuàng)新。對于企業(yè)來說,改善是永無止境的。了解了TPM管理的基本內容,理解了TPM管理的指導思想后,TPM管理是什么的問題即使應用不同,也可以更深入地分析公司的環(huán)境場景,有利于開發(fā)應用TPM管理活動。
企業(yè)為何要融合精益與TPM?以上就是新益為TPM咨詢公司的相關介紹,做好企業(yè)的TPM管理工作就是為精益生產管理活動打下基礎,讓精益生產管理在企業(yè)中發(fā)展有一個良好的前提。
建立生產有序、管理順暢,操作規(guī)范,士氣高昂、高質量、低成本、短交期的作業(yè)現(xiàn)場;
為企業(yè)規(guī)劃設計一套由內到外的形象升級,外觀視覺價值體現(xiàn)、內在的管理內涵體現(xiàn);
全員參與設備管理高產出和低成本運營,提升設備管理能力,維護能力,提高效率
構建班組生產管理體系、循環(huán)評價、人才育成、持續(xù)改善、績效管理、文化養(yǎng)成體系;
提高產品質量、降低生產成本、縮短交期、增加利潤,讓管理更系統(tǒng)科學,執(zhí)行力更強
對工廠的各個組成部分進行合理安排,以提高生產效率、降低成本、優(yōu)化物流、改善工作環(huán)境等